Case study
Single Motor Maintenance Fix Saves Nuclear Facility $150,000
The Primary Challenge
Nuclear power plants operate with complex processes in a stringent regulatory environment. When these facilities schedule seasonal routine maintenance outages, it’s during times when the demand for power is near its lowest and the facility can operate considerable lower than 100% capacity.
As a major nuclear power facility prepared for a planned outage, its maintenance team conducted testing on one of its four 1,250-horsepower C-heater motors. Multiple test results were inconsistent but suggested that the motor – which weighs about 20,000 lbs. or the equivalent of four average-sized pickup trucks – had experienced ground fault damage. The maintenance crew engaged Smith Services to perform a motor rewind to correct the damage.
The motor was removed and sent to Smith Services’ 180,000-square-foot repair facility in Princeton, W. Va., for rewind. After conducting their own inspection and high-voltage motor testing, the Smith Services team found no issue with the windings. The motor was cleaned out and then dried in an oven to remove impurities, then retested again with passing results.
Doug Mitchem, district manager for Timken Power Systems, says the customer’s initial misdiagnosis was due to tight quarters in the nuclear power facility. “They lacked the space needed to fully dismantle the motor and assess the entire system, which we had the room to do in our shop,” he says. “Once we fully inspected the motor, we found the failure occurred in the leads coming out of the stator frame. The insulation had failed as the leads rubbed against the frame, causing the leads to cut on and off intermittently.”
The Solution
Smith Services recommended that the motor be re-leaded and undergo a stator refurbishment – a fix available at a fraction of the cost of a motor rewind. When the nuclear power facility’s maintenance team learned about the new diagnosis and solution, they asked Smith Services to provide an additional solution the plant team could do themselves to prevent similar issues on the other three motors still in operation.
“We manufactured and installed a G-11 insulator, similar to glue, for the first motor we repaired,” Mitchem notes. “It holds the leads in place, keeping them from moving around and getting back inside the stator. Then we manufactured a two-piece insulator for the remaining three motors that wouldn’t require major disassembly of the outer jacket to install. This essentially became a maintenance kit the customer’s team could use to fix the remaining units in their facility.”
A Smith Services technician visited the nuclear power facility to instruct its maintenance team on how to apply the solution. “They were shocked at how quickly we were able to demonstrate the new lead solution. We probably weren’t on site an hour,” Mitchem says.
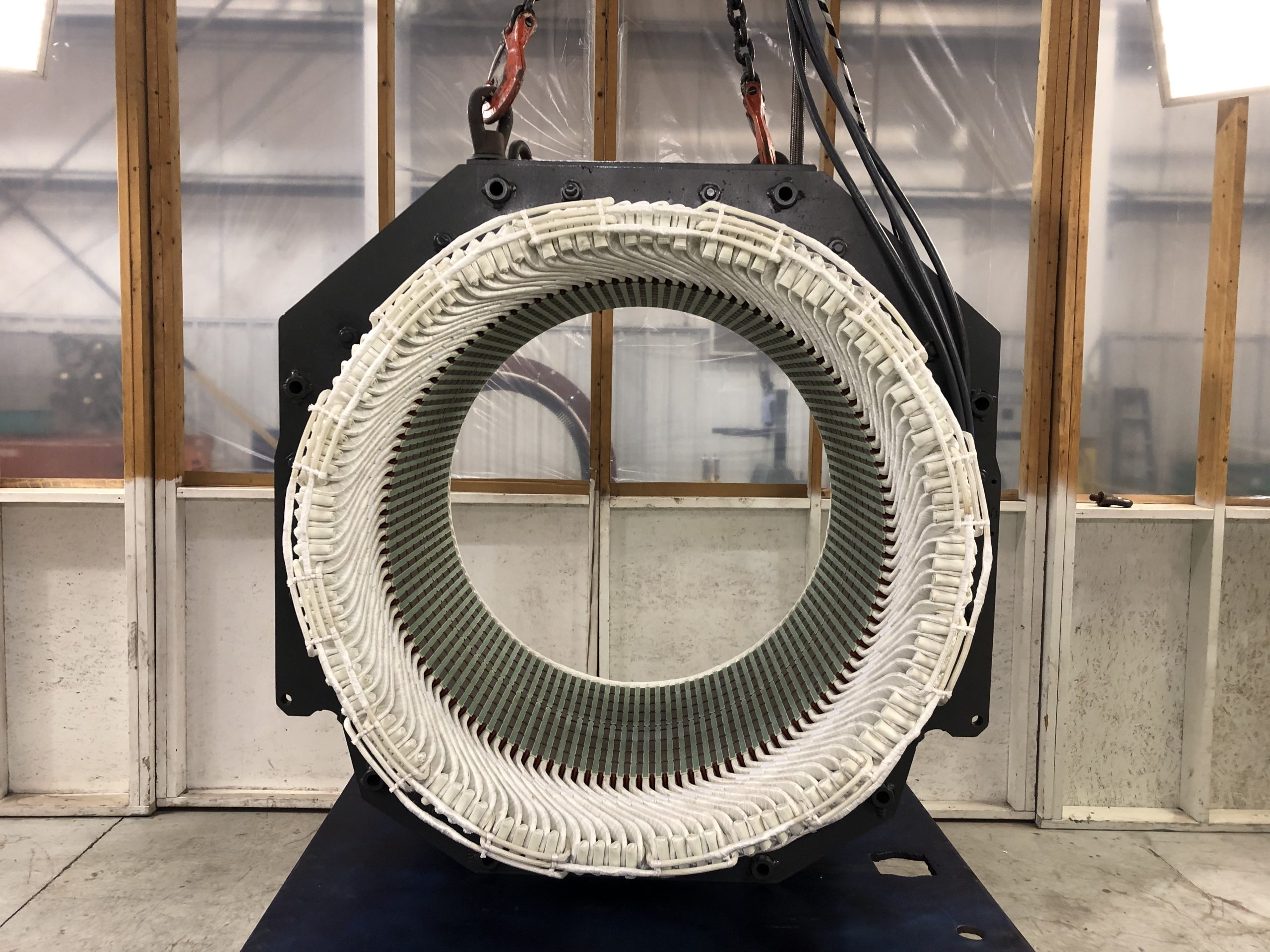
Key Results
The nuclear power facility planned to spend about $80,000 to solve a misdiagnosed problem. The Smith Services inspection led to a re-lead and refurbishment solution that cost just under $50,000. By preventing future failures and repairs on the three other motors, including associated crane and manpower costs to remove them in the future, Smith Services saved the customer approximately $150,000.
“I’ve been in the motor business for more than 20 years, and I’ve seen shops rewind motors that really don’t need to be rewound,” Mitchem says.
“At Smith we hold ourselves to a different standard and there’s a lot of integrity in what we do.”