Case study
Collector Ring Repair Upgrades Steel Plant Equipment and Restores Operations
Smith Services’ Unique Collector Ring Repair Service Helps Upgrade Steel Plant Equipment and Restore Critical Operations
A large steel plant located in the Midwest region contacted Smith Services when they experienced a failure in one of their electric motor and generator sets. The 800 horsepower motor-generator set is one of four large synchronous drive motors that operate critical production line electric motors for the steel plant’s galvanized coating process.
Smith Services deployed the field service team to the customer site, and the electric motor and control systems were inspected to determine the cause of the failure. They identified the problem as an electrical failure at the collector rings (also known as slip rings). Contamination of the laminate material used for insulation on the collector rings and a faulty contact on the field discharge resistor in the electric motor control system were the causes of the problem. The field discharge resistor failed due to a high voltage spike in the rotor circuit. This, combined with laminate material contamination, caused the collector rings to fail ultimately.
“Most electric motor repair companies would just fix what failed and return the motor to OEM condition,” said Adam Watts, engineering manager for Smith Services. “At Smith Services, we take it a step further (whenever possible) and pride ourselves in performing failure analysis. We not only repair electric motors quickly, but we also present customers with innovative solutions. Leveraging the latest technologies, insulation systems, and manufacturing techniques, we engineer long-term and reliable solutions so customers can get the most out of their equipment,” said Adam.
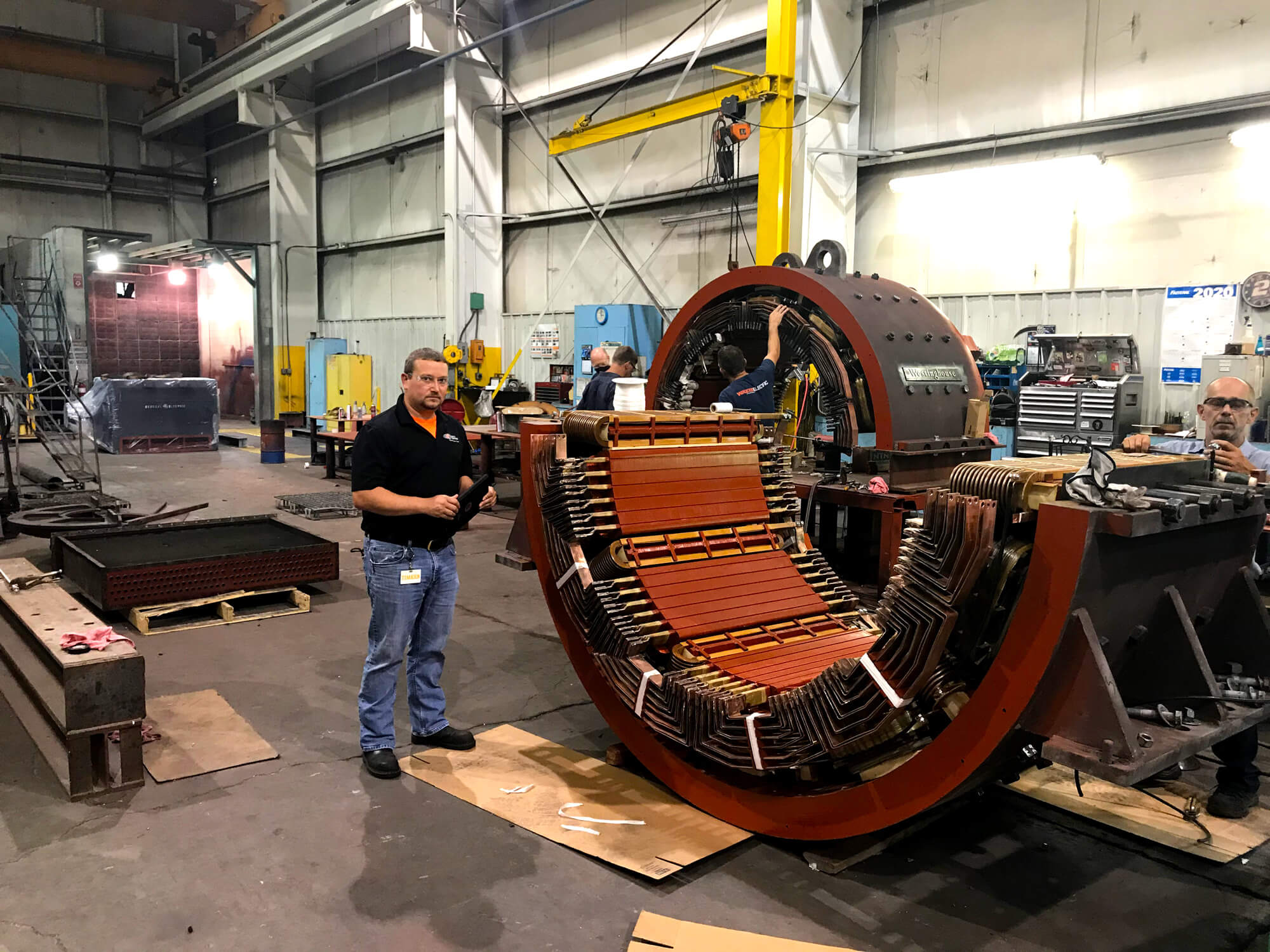
And in the case of the equipment failure for the steel plant, doing an upgrade for the customer was no exception. In addition to repairing the control system components, Smith Services offered the customer a collector ring upgrade featuring an innovative split-ring configuration that allowed for easier, in-place maintenance and replacement without having to remove the equipment from service.
The new collector ring design featured non-porous, chemical-resistant insulation material with increased dielectric strength to combat particulate contamination. Additionally, the new system included a spark-gap safety that provided a method to effectively dissipate the energy generated in the field circuit during motor start-ups should the field discharge resistor fail in the future.
After evaluating Smith Services’ proposal, the customer elected to perform the repair and upgrade on the large generator. The large motor-generator set repair was completed on-time and remained in service, running flawlessly for six years until the next scheduled routine bearing maintenance (which typically includes a collector ring replacement). During routine maintenance, they found that the upgraded collector rings installed six years earlier were still in good condition, did not need replacing, and were fit for continued service.
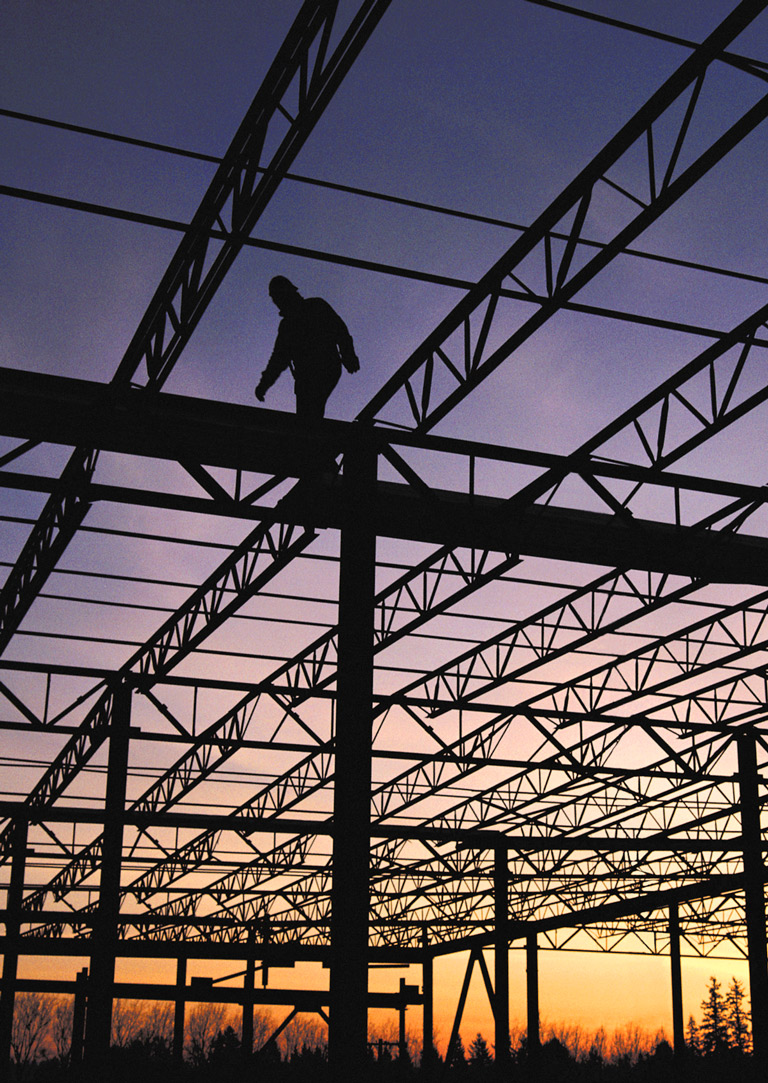
This design upgrade to the customer’s critical generator in the steel plant has proven so successful and reliable that they contracted Smith Services to install the collector ring upgrade on all four large electric motor-generator sets. Due to their increased reliability, a significant reduction in unplanned outages from collector ring failure has drastically reduced the customer’s total plant ownership cost. “This collector ring design upgrade is an excellent example of how our partnership with our customers can result in long-term reliability improvements and cost reductions,” said Henk de Swardt, chief engineer – electrical for Timken Power Systems.
The collector ring upgrade described in this case study is exclusively available from Smith Services. To learn more about how our engineers install the upgrade and how it can help improve your electric motor and generators, see our collector ring services page.