Case study
Cement Mill Reconditions Over a Dozen Coal Mill Rollers in Only Nine Days
Working around the clock, seven days a week, a major cement mill located in the Mid-Atlantic region of the United States produces over 4,000 tons of cement each day. Spanning over 100 acres, the mill is part of a network of U.S. plants that produce more than 100 million metric tons of cement each year.
Tasked with turning huge chunks of quarried limestone rock, sometimes as large as a grand piano, into the marble sized “clinker” that eventually becomes cement, the plant operates massive machinery under some of the most extreme conditions and dirtiest environments in the cement industry. Whether it’s a 400-foot kiln operating at 2,600°F or a large raw mill that produces the millions of pounds of thrust required for turning bare rock into raw mix, maintenance personnel are under constant pressure to ensure that all mission-critical equipment runs smoothly to avoid downtime that could cost them hundreds of thousands of dollars per day.
In the first quarter of 2019, Smith Services was called upon to assist the plant during a planned outage to perform scheduled maintenance on aging equipment that would need to be in good operating condition as they were about to enter their busiest season. An electric motor and gearbox repair facility, Smith Services has also established a long-standing legacy of supporting the needs of the cement industry by specializing in mechanical repairs for raw mill rollers and rotary feeder boxes, stacker car wheels, clinker breaker shafts, coal mill rollers and table assemblies, rocker arm assemblies, primary fans, and other critical components. Because of an over 20-year successful working relationship with the plant, Smith Services was awarded the project due to their track record of providing exceptional service during plant outages, and in times of emergency when production was at a standstill caused by equipment failure.
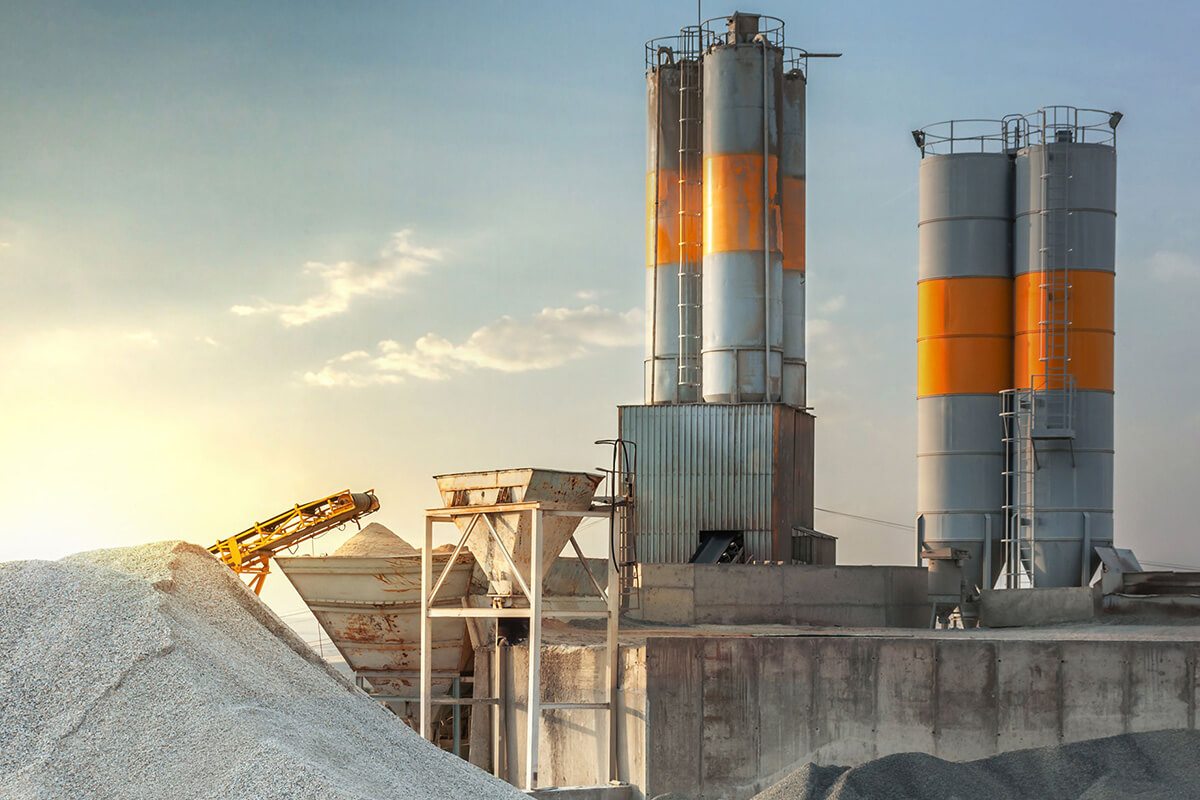
To perform the required maintenance, plant technicians took six coal mill rollers and eight raw mill rollers out of service, and sent them to the Smith Services manufacturing facility in West Virginia for inspection and reconditioning. During the same time period, the customer also requested a crew of On- site Technical Service (OTS SM ) personnel to be sent to the mill to work with their maintenance team to inspect several other pieces of equipment, and perform in-place repairs where necessary. “We’ve been working in the cement industry for over two decades, so this type of repair is common for us,” said Ellis Martin, quality and operations manager for the Smith Services facility. “What made this project unique was that the plant’s heavy production period was unexpectedly extended by a week due to some favorable weather. That pushed back the planned outage start date and shortened it to only nine days.”
The Smith Services team had already staffed and prepped to disassemble and inspect each unit as soon as they were received at the shop. That enabled them to get an inspection report in the hands of the customer as soon as possible to allow them to quickly approve the scope of repair. “By the time raw and coal mill rollers reached us for repair, many of them were badly worn and caked with layers of dust and grime from the punishing manufacturing process,” said Chris Buckner, production manager for Smith Services. “To meet the customer’s deadline, we worked around the clock to flush, clean and examine the components. Our inspection process included a complete breakdown of the unit, which involved removing all bearings, measuring the housing, and performing a thorough mechanical evaluation to determine what parts could be salvaged and what needed to be replaced in order to restore them to top operating condition.”
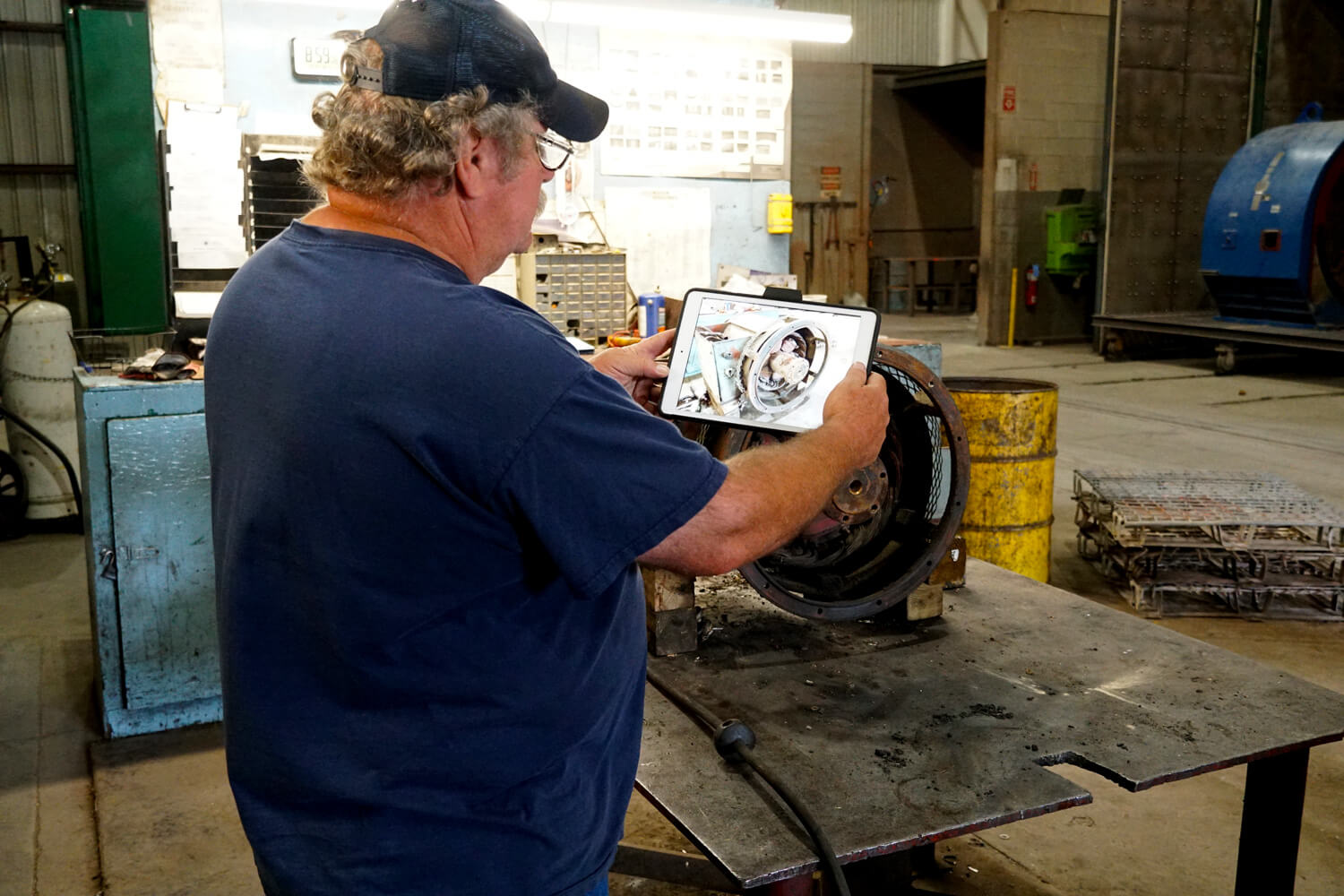
Each of the six coal mill rollers exhibited varying stages of wear and required slightly different scopes of work. The repairs made to the rollers included a combination of installing new bearings and seals, polishing the mechanical fits for the seals, bearing journals and bearing housings, and repainting the units in preparation for final delivery. In addition, it was discovered that on one unit, the integrated arm that swings the roller mill down on the crushing table to smash the coal was damaged and needed replacement. Because the expected scope of work had grown considerably, the customer agreed to a longer lead time due to parts availability and the complexity of the repair.
More challenging to disassemble and service due to their sheer size, weight, and complexity, the eight raw mill rollers took more time to inspect and required varying degrees of overhaul. Some of the repairs done on the damaged rollers included: installing new top seal caps and t-bolts, machining and fitting new thrust collars, replacing old rock guards with new ones, and installing new seals and O-rings. “Weighing close to 26,000 pounds each, just handling the logistics for the transportation of the raw mill rollers can present a challenge for other facilities that aren’t prepared for this kind of work,” Ellis continued. “Our shop has been handling repairs of this size for more than 20-years, so we’re well outfitted to service this kind of equipment. In addition to all of the smaller repairs made to the raw mill rollers, we’re equipped to do complete maintenance on these units, including the full replacement of the tires, skirts, and caps that we ended up replacing on some of the old rollers that were part of the outage.”
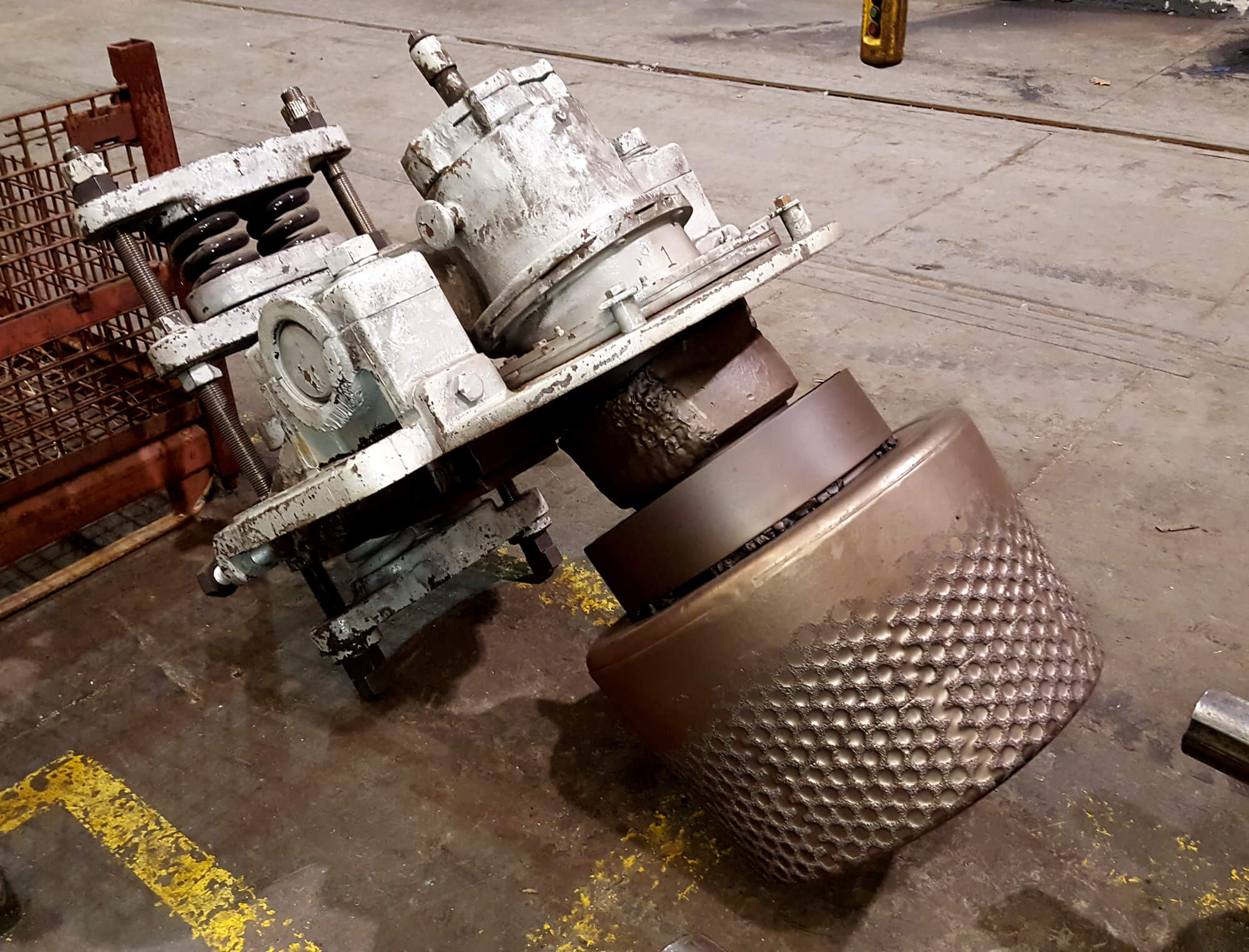
While the work was occurring in the shop, Smith Services’ OTS team was deployed on-site, and coordinated their activities with plant technicians to inspect other critical equipment used throughout the mill. “Working 12-hour days for more than two weeks, our field technicians inspected over 20 fans that were relied on to help cool various equipment, from raw and coal mills to kilns to air preheaters,” said James Kline, manager of field service for the Smith Services facility. “Our crew has built a great relationship with the plant over the years and has become a trusted adviser to the point where we’ve become a critical extension of their workforce. What sets us apart is our willingness to ‘run to the problem’. We provide expertise for repairs that they either don’t have the time or manpower to do, such as inspecting and replacing bearings and seals, installing gearboxes, performing laser alignments and providing balancing services for critical components for virtually any of the equipment in the plant.”
The two-week OTS team’s scope of work included replacing fan bearings, removal and replacement of complete fan assemblies, replacing fan belts and wheels, and realigning fans that were out of specification. “There were many moving pieces in this project that required the involvement and coordination between several key people in our shop, the OTS team, engineering, and maintenance personnel at the mill,” said Mike DiGiacomo, plant manager for Smith Services. “We were able to deliver the remanufactured rollers and complete all the field service work on-time, and a week ahead of their normal schedule, with the exception of the one unit that was waiting on parts to repair the roller arm. The long lead times associated with purchasing new equipment of this type is not a viable option for a busy cement mill, so we’re thrilled to be able to provide them with a much quicker solution and help get them ready for their busy season without them incurring unplanned downtime.”