Case study
Getting a Large Paper Mill Back Online After a Lightning Strike
Like in many other industries, facilities in the pulp and paper market are accustomed to a readily available supply of off-the-shelf, standard electric motors when the need for a replacement arises. For the most part, this is made possible due to the well-established NEMA (National Electrical Manufacturer Association) electric motor standards. However, when a critical motor in a power converter in a Virginia paper mill experienced an electrical surge from a lightning strike during a severe thunderstorm, the mill was in jeopardy of a long-term shutdown when no off-the-shelf replacement was readily available.
The paper mill was built in 1899 during a time when 25 Hz was a standard alternating current (AC) utility frequency in the United States. The standard’s origins trace back to the first generators at the Niagara Falls hydroelectric generating station, built by Westinghouse in 1895, where 25 Hz was the optimal utility frequency to run the turbines. The project eventually proved so influential on electric power system design that 25 Hz prevailed as the North American standard for low-frequency AC. As a result, much of the paper mill’s equipment was built around this specification.
In decades to follow, the United States gradually moved away from 25 Hz to what has become a 60 Hz standard, and by 2006, the utility supply of 25 Hz was discontinued. To meet this new standard, the paper mill was facing the crippling financial reality of replacing all of their outdated equipment, which could have resulted in the plant’s closure. Looking for other options, the paper mill contacted Smith Services. The Smith team located a 1940s-era, 26,000 kVA motor-generator set that they refurbished, retrofitted, and installed to solve the plant’s problem. The upgraded and improved equipment consisted of two large synchronous motors coupled together and designed to function as a power converter to transform the 60 Hz utility frequency to the 25 Hz needed to keep their existing machinery running. The project was a success. Smith Services’ creative electric motor repair solution saved the plant millions of dollars in equipment replacement costs and the countless months of downtime that could’ve resulted in their closure.
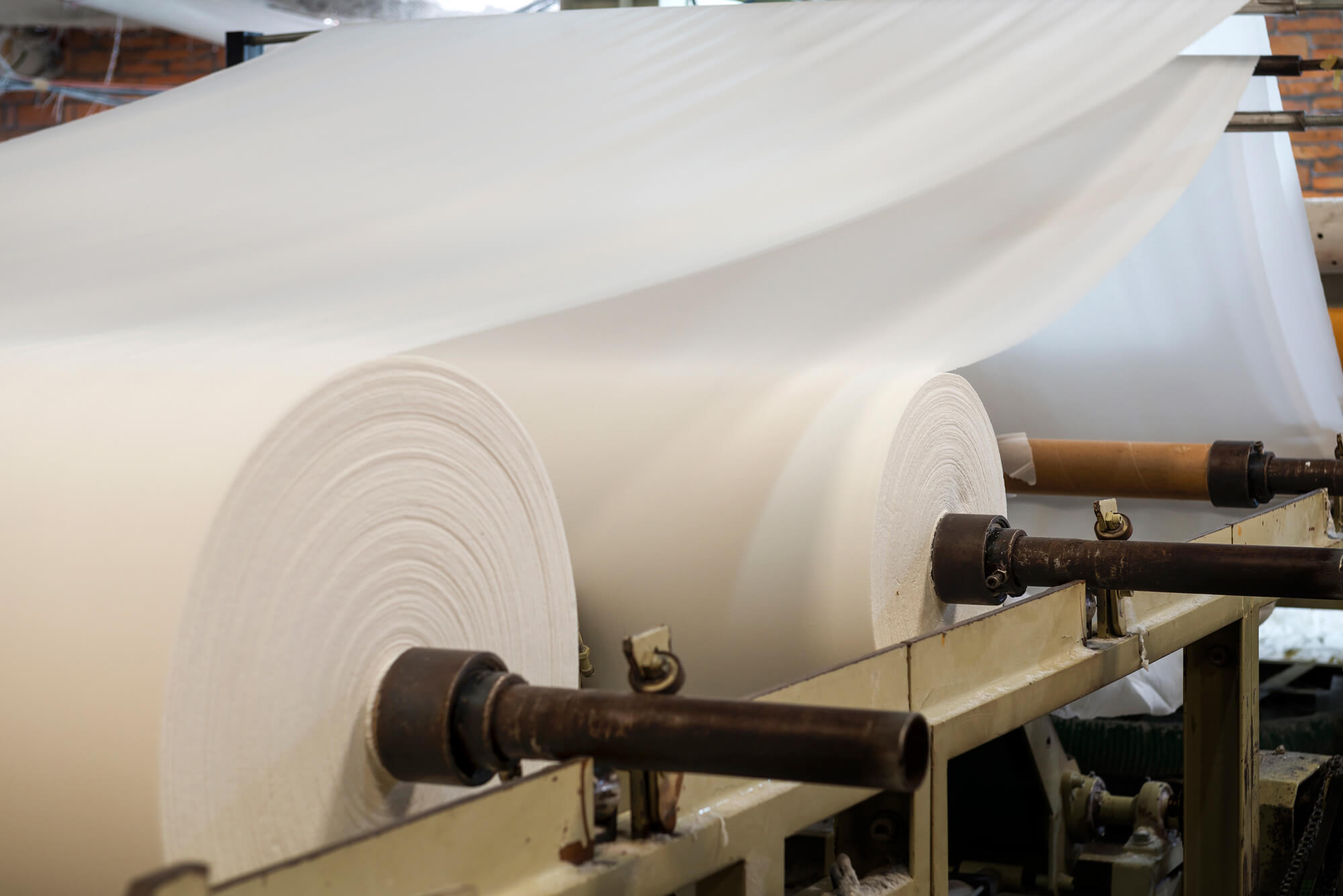
The repaired electric motor and generator set ran faithfully from the time of its installation in 2006 until June 2020 when a severe thunderstorm struck the area and brought the plant’s production to a standstill. As a large part of the local economy, the paper mill employs a fifth of the local town’s over 5,000 residents, so the shutdown prompted an emergency call from a distressed Maintenance Superintendent to Smith Services for help.
Smith Services immediately mobilized emergency field service technicians to do an equipment inspection at the customer’s site. As indicated in the initial phone call, the Smith team confirmed that an electric motor suffered a current differential trip on the C phase during the thunderstorm. The motor portion of the motor-generator set is a massive General Electric 34,200 HP, 13,800 V, 3-phase, 300 RPM electric motor. The C phase of the motor winding was found to be short-circuited to ground and was determined to be unrepairable. A detailed inspection did not reveal the typical burnt hole in the winding that’s common with this type of failure. “This situation immediately brought to mind many scenarios we’ve encountered where a severe thunderstorm led to a lightning strike that damaged equipment. We suspected that also could be cause for the equipment failure in this situation,” recalls Adam Watts, engineering manager for Smith Services.
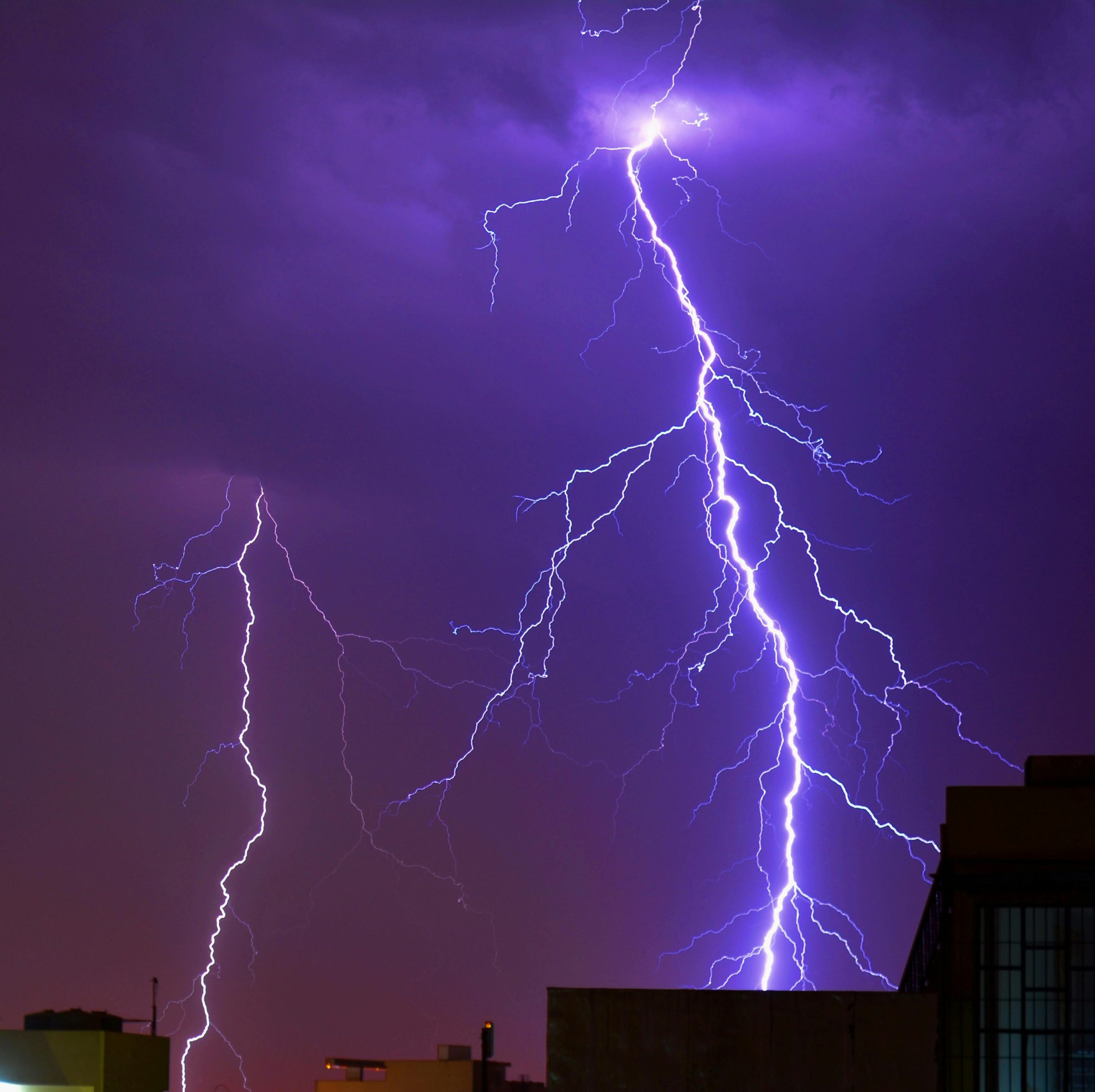
After the initial consultation, Smith Services assembled an emergency response electric motor repair team that included experts from their Engineering and Field Service departments. The electric motor repair plan consisted of gathering winding and connection data, isolating the coils of the C phase to identify the faulty one, bypassing the bad coil, and bringing the power converter back online. “Naturally, we knew that a modification of this type to the original equipment would change its performance. So we presented detailed models and performance parameters to plant technicians for them to determine if the system would perform well enough and function within the specifications that they needed to restore the mill’s production line to full operation safely,” said Adam.
After receiving customer approval late at night on day two of the shutdown, the Smith Services team arrived in the early morning hours on day three to begin the electric motor repair. Technicians gathered winding and connection data from the motor-generator set, allowing their engineers to create a connection diagram as a guide for isolating the 66 coils of the C phase, which consisted of 3 parallel circuits containing 22 coils each. Without knowing any other information, they would have had to disconnect each coil and test them individually. And this procedure would have taken the field service technicians more than ten days to complete and resulted in a substantial increase in production losses. “Experience from working on prior lightning strike events taught us that the first coil in a line connected group typically takes the brunt of the energy from an electrical surge of this type. Also, the line connected coil closest to the supply lines or buss is usually the likeliest suspect for coil damage of this kind,” explains Adam Watts.
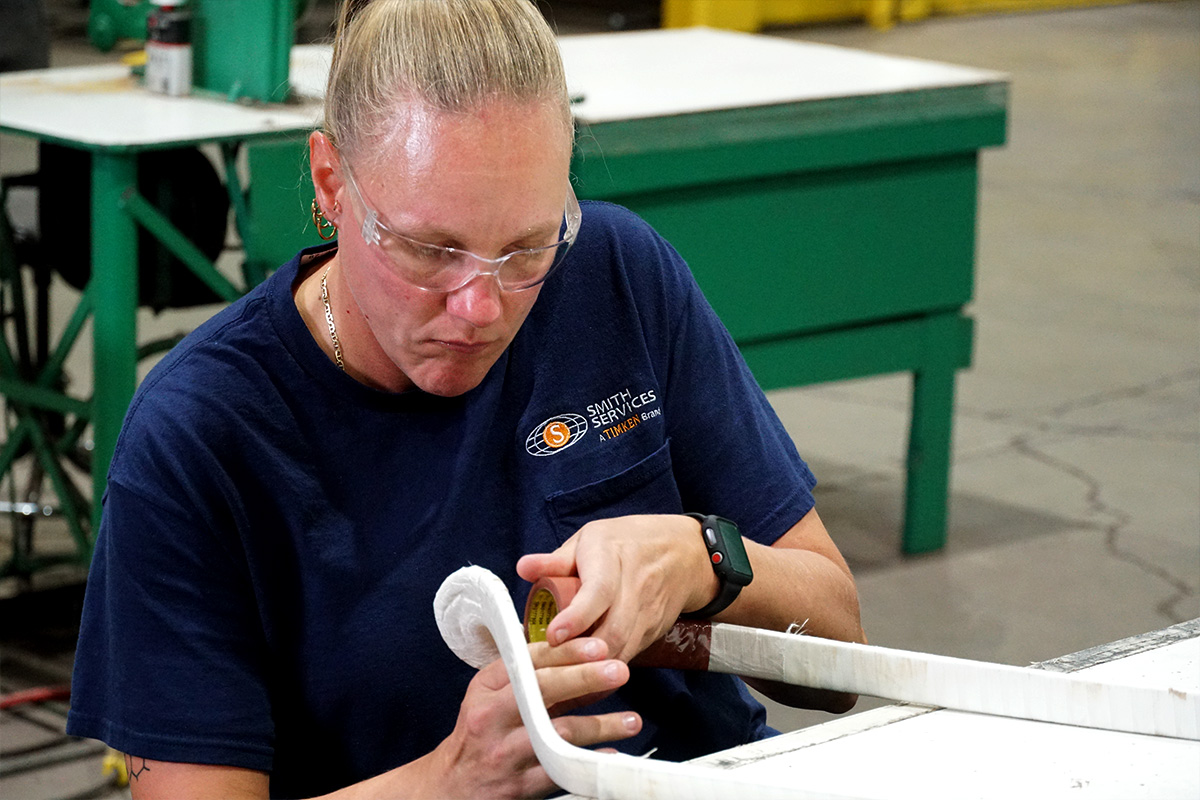
The assumption proved correct. When technicians inspected the line connected coil in the bottom portion of the stator winding directly adjacent to the incoming supply buss, they found it was damaged by the lightning strike and caused the failure. Smith Services’ electric motor repair experience proved invaluable, saving potentially weeks of diagnostic time and significantly shortened the overall repair time.
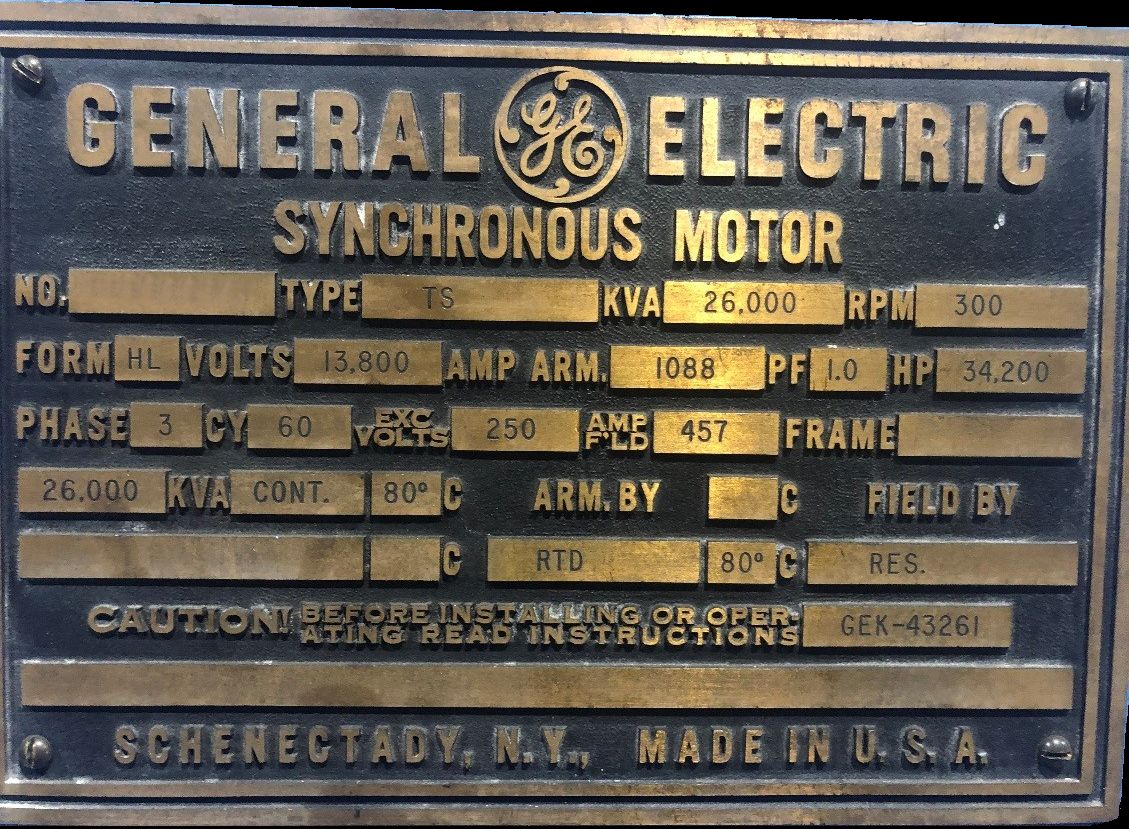
By midday on day four, the Smith Services team completed the failed coil bypass, proof-tested the winding, and released the repaired unit to the plant, allowing them to resume full production a week ahead of schedule. “Giants of industry like General Electric, Westinghouse and Allis-Chalmers helped build a legacy of machines that supported the growth of manufacturing in the United States,” said Henk de Swardt, a chief electrical engineer for Timken Power Systems. “They are from an era of machines designed with huge safety margins, and like in the case with the paper mill, with a little loving care and expertise, old equipment, once written off, can often be returned to service. And with new upgrades like improved insulation systems, sometimes it can even perform better than how it ran originally, giving the equipment a new life for many years to come. That’s not something you can often say or come across in modern equipment designs,” finished Henk.
“Smith Services has been serving customers across the US with the goal to help them maintain peak production – even when disaster strikes,” said Adam Watts. “Experience is not taught. It’s gained by running to the problem, by being a regular presence in our customers’ shops and listening to them and understanding their requirements, and then developing and implementing the right engineered solution to fit their needs,” finished Adam.