Case study
Aluminum Recycler and Producer Avoids Costly Downtime with Electric Motor Repairs
The Primary Challenge
Aluminum is one of the world’s most recyclable materials and an ideal solution for a more circular, sustainable economy. A leading aluminum recycler and producer with operations throughout the U.S. recycles the equivalent of 20 billion cans annually at just one of its facilities. The plant, which is one of the world’s largest recyclers of used aluminum cans, crushes and melts cans down to support production of new sheet products for beverage packaging and aluminum coil for automotive applications.
The manufacturer uses multiple crushers in its massive recycling operation, each driven by approximately 20-year old 1500 HP synchronous electric motors. The facility’s maintenance team noticed arcing and performance issues in one of the crusher motors and suspected faulty collector rings, or slip rings.
“Slip rings are electromechanical devices that facilitate the passage of an electrical current through a rotational joint. They are crucial for efficient operation, productivity, and uptime,” said Eric Farrington, principal sales representative at Smith Services™, a Timken Power Systems company. “If one of these motors fails, it creates a dual threat of lost productivity: first in recycling operations and also by holding up new aluminum production.”
Even though the maintenance team had a spare motor to swap in for the failing motor equipment, they were eager to get the first motor repaired quickly because one of the bearings in the recently installed spare motor was displaying signs of a thermal issue. The team was concerned this could lead to the spare motor’s failure, causing downtime while the first motor was out for repair.
Due to a 25-year relationship and a positive experience with a motor rewind for a different crusher motor just a few months prior, the customer contacted Smith Services for assistance.
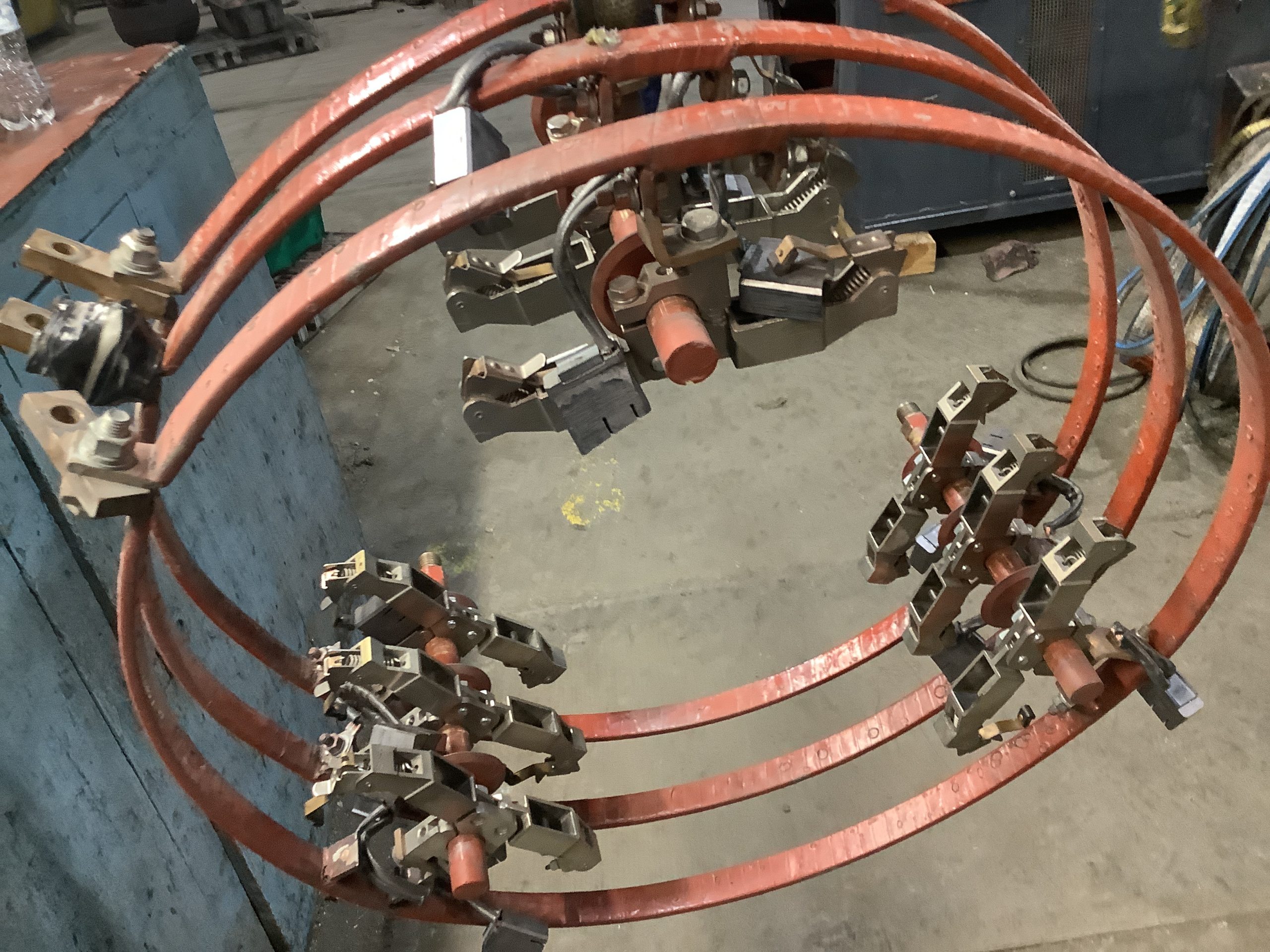
The Solution
Within hours of receiving the call, Smith Services dispatched a truck to pick up the motor and transport it more than 500 miles to its electric motor repair facility in Princeton, West Virginia, with more than 180,000 square feet of space under one roof, it is one of the largest and best-equipped motor repair facilities in North America.
Smith Services immediately began disassembling the unit and thoroughly cleaned and visually inspected all parts. Inspection revealed several issues. Some of the slip ring brushes were lodged in their holders, which prevented proper contact with the surface of the slip rings. One of the conductive surfaces of the slip ring was heavily discolored and burnt, which was an indicator that the brushes were not making proper contact with the ring. In addition, the bearings lacked proper lubrication.
All critical mechanical components were dimensionally inspected to ensure integrity and compliance with industry standards. The Smith Services team reassembled the motor using all repaired parts and several new components, including brushes, a cylindrical roller bearing, lugs. From start to finish, Smith Services reconditioned the motor around in just three weeks.
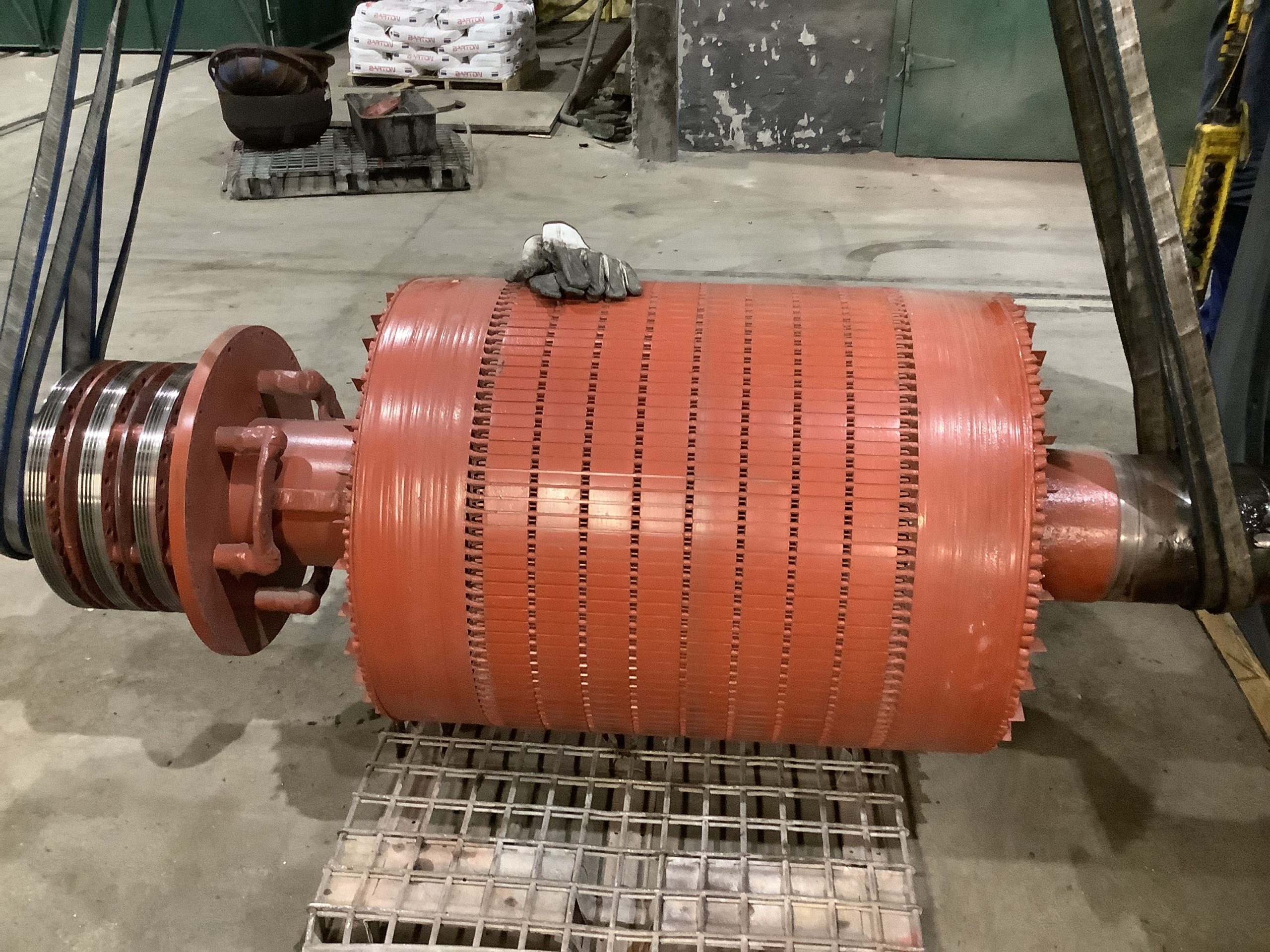
Key Results
“This plant knows our capabilities and track record with these motors,” said Farrington. “They trusted us to get the job done and routinely come to us with their most challenging motor repair needs.”
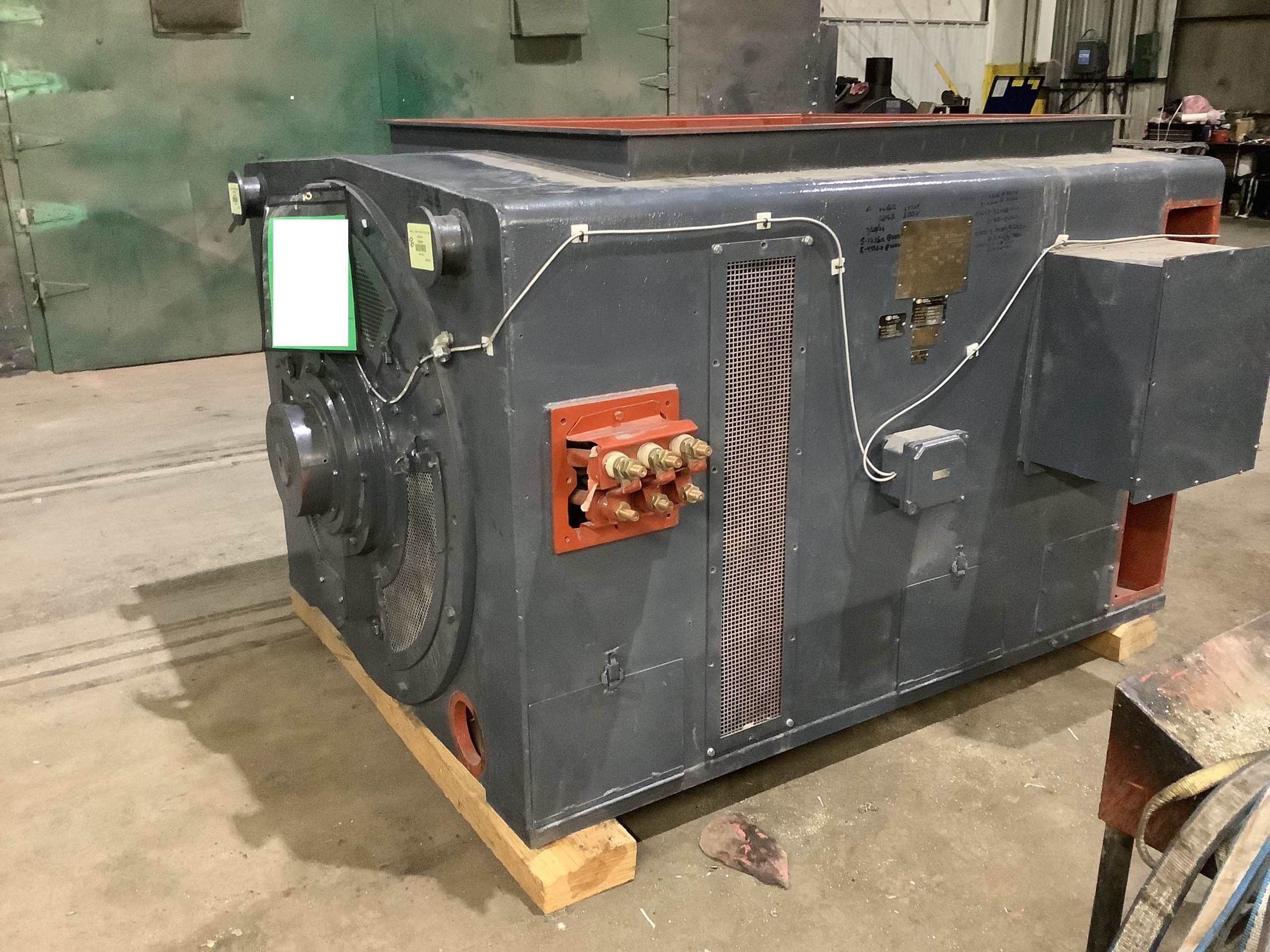