Case study
Smith Services’ Medium Voltage Motor Repair Capabilities
We interviewed Adam Watts, engineering manager at Smith Services®, a leading industrial motor repair facility, to discuss medium voltage industrial motors and motor repair.
Q: Adam, can you tell us more about what you do at Smith Services, what your position is?
A: I am the engineering manager, I manage the day-to-day engineering activities from an electrical and mechanical standpoint. I am duel-degreed, electrical and mechanical, and have been with Smith Services for over 20 years.
Q: What makes Smith Services different?
A: If we went to the EASA (Electrical Apparatus Service Association) website, you will see that they are a pro-customer and pro-service center intermediary. They help write specifications and standards for governing electric motor repair or electrical mechanical equipment that puts everyone on common ground from the end-user to repair centers. If we searched that website, I bet there would be in excess of 1,000 service centers in the United States. Service is a local business. Smith Services is set apart from others by our size. We are the largest electric motor repair shop on the eastern-half of the country. All of our sites are members of EASA, which is a big deal. We are very active in it. It is something you must have to be a player in the market.
Q: Tell us about medium voltage motors.
A: What constitutes a medium voltage motor is a voltage rating of 2,300 volts, or greater than 1,000 volts and up to 13,800 volts. From an industrial perspective, your smaller applications, sub-hundred horsepower applications and below, are typically powered with 240 volt or 480 volt motors, some relatively common industrial voltage. When you start getting into the larger horsepower equipment, it becomes cost prohibitive to operate those at lower voltage ratings.. The higher the voltage rating, the lower the current rating. Reducing the current rating reduces the size of the conductors that are within the motor or the conductors that connect the motor to the power source. All of this reduces the need for materials, but it does require more insulation to protect it from that voltage. By going with higher voltage systems, you reduce the losses and increase efficiency of the process. Reducing the current lowers the losses by the square of your reduction. Gains could be exponential.
Q: What are the most common applications for medium voltage motors?
A: Medium voltage motors start to show up in the couple-hundred horsepower applications, somewhere around 200-300 HP range, up to 700 HP. In that range, you still have an even mixture of low voltage or sub-600 voltage equipment, and greater than 1,000 volt equipment. Once you break that horsepower threshold, the vast majority of the motor applications are medium voltage or greater. But there aremany applications where you would find a medium voltage motor. You start to see the efficiency gains are substantial, most commonly used for mission-critical applications.
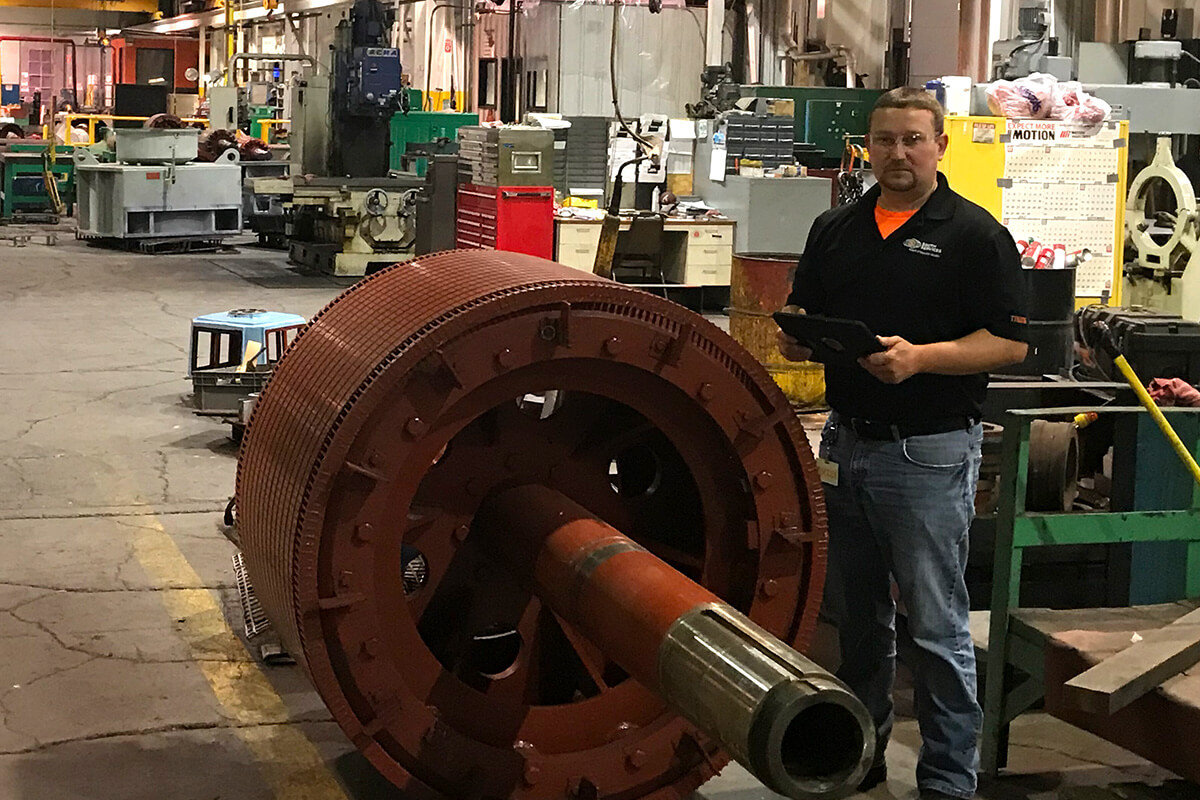
Q: What are the main drivers when a manufacturer is selecting the right motor for an application?
A: If we look at it from a high-level, the main thing a manufacturer would need to determine the proper motor selection is the type of application. Is it compressor duty, a pump application? Pumps and fans have special requirements, compressors typically live a hard life so there are a lot of thermal concerns that go into motor design. Belt drive applications, where there’s a significant amount of radial loading, requires special mechanical engineering and design aspects. Or it could be some exotic equipment like centrifuges that have special design requirements that go into motor selection. The primary concerns are the details of the application. Understanding this is the key to get a good idea of what the requirements are and must be put into this equipment.
Q: What industries would you find a medium voltage motor?
A: I can’t think of any major industry that does not have medium voltage applications; you will absolutely find medium voltage equipment in the petrochemical, pulp and paper, metals manufacturing, and power generation industries. Some plants, depending on the geographic location, have more than others. If they are new, they will select a place on the power grid that would allow them to leverage the advantages you’d get from medium voltage applications. If you go back 50 years, they would build pulp and paper mills in areas that were centrally located near water sources with less regard to power infrastructure.
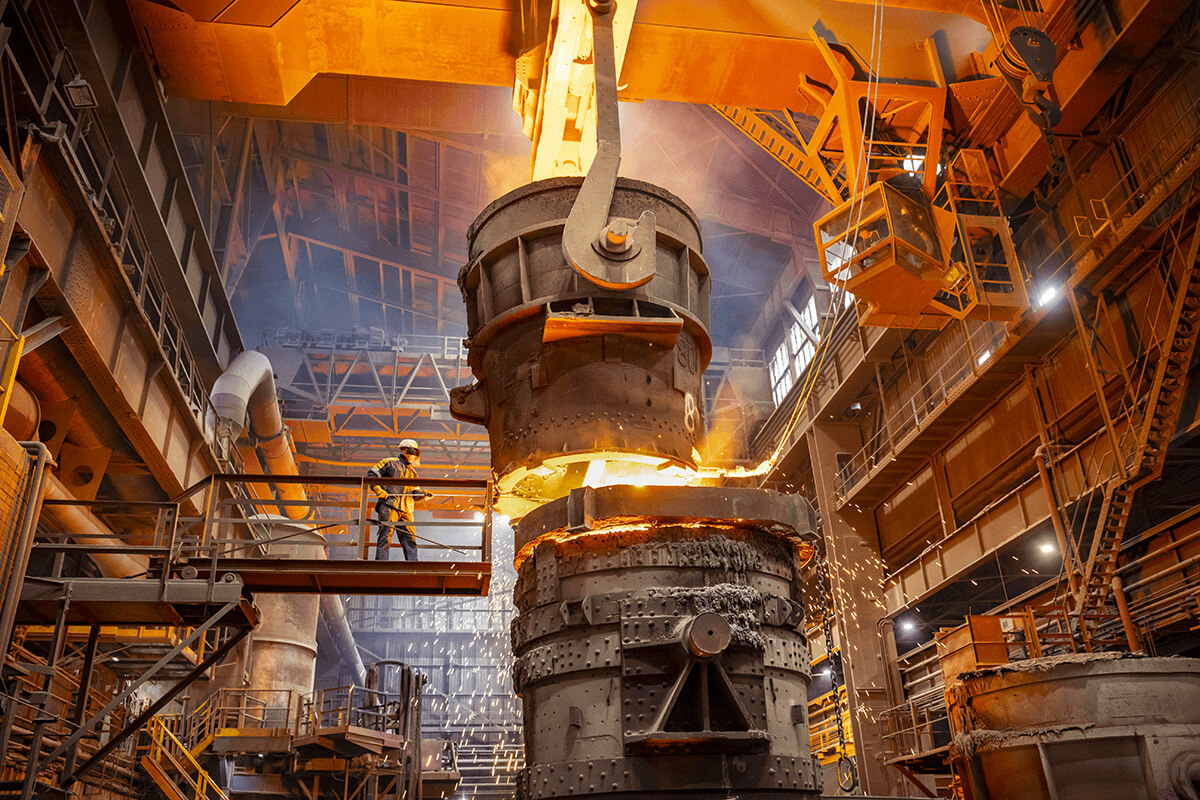
Q: How many other motor repair facilities handle repairs to medium voltage motors?
A: Our ability to service medium voltage motors removes roughly half of the competition in this market. Then, by region, this number shrinks a lot since it is often based on location. Some competitors service high voltage equipment, rated much higher than those at 13,800 volts. These are much more rare due to efficiency gains, but right now the medium voltage market is the biggest opportunity. From repairing large motors to servicing the switchgear that powers the large motors, that is one of the things that sets us apart. We have our own people on staff that go out to troubleshoot the breaker systems, transformers, performing the necessary electrical tests, and we can do it all on-site or in-house. Some large motor repair can also be completed on-site, while a full gamut of large motor repair or large generator repair can be done in-house for the medium voltage equipment. While we are very focused on electrical motor repair, servicing the driver, switchgear, and repairing the transformer, are also other parts of the puzzle that we can service. All of the large motor facilities in the Timken Power Systems’ network service medium voltage motors and equipment. Within eight hours, we can service nearly three-quarters of the eastern United States.
Q: Any specifics on load testing and spin test capabilities for the facilities?
A: In order to test medium voltage motors, from a testing standpoint, a validation test, you have to have power sources available to apply them to that particular large motor. This is one of the things that reduces the amount of competitors. In our Smith Services facility we have a dedicated 2,500 KVA test center. We can test 13,800 volt, 7,200 volt, 4,000 volt, and 2,300 volt, all of the medium volt classifications. Our dynamometer capacity is 12,000 lb-ft of torque which equates to 2,500 HP at 1,200 RPM. A 5,000 HP motor can still be load tested at proportional values with a full complement of documentation.
Q: Can you tell us about your warranties and maintenance?
A: From a warranty perspective, we do not differentiate between low voltage or medium voltage. We are comfortable with our motor repair services so our warranty remains the same for the two. You get up to 6 months on the shelf, and a year in service regardless of large motor or large generator ratings. The only exception to this was for a short term, there were some manufacturers that were making random wound equipment in medium voltage, and they were only doing so in a 2,300 volt class. OEM’s really pushed the design envelope making those motors notoriously difficult to repair. With increased voltage, there is an increased requirement to contain that voltage, and that is where that added insulation materials come into play. Advances in insulation material technology has allowed for more reliable repairs. From a maintenance standpoint, cleanliness is key. Routine inspections of your large industrial motors, if they are dirty then they need to be cleaned, whether it is a simple blow down or inspection, and routine electrical testing can help indicate when you have a cleanliness problem. You can also use this data as predictive maintenance in scheduling outages or inspections on site before removing for repair overhaul. This would be even more so with these types of large motors and applications. The higher the voltage rating goes, the lower the current rating, and while you increase efficiency, you also increase the need for more insulation to contain that voltage or pressure that is continuously trying to escape.
Q: What is the relationship between the footprint of the equipment, the voltage rating and horsepower rating?
A: The driving factor behind the footprint is torque output. You could have a 100 HP large motor that is rated for 1,800 RPM, that’s 300 pound-feet of torque. If we change the speed rating on that motor down to 300 RPM, with the same 100 HP motor, then it can produce almost 1,800 pound-feet of torque. With that, mechanical load requires more mechanical structure. The speed rating and torque output is what drives the footprint of a motor.
Q: Anything else you would like to add, Adam?
A: I would strongly recommend routine inspections, cleaning, vibration monitoring, and electrical testing as part of predictive maintenance which are key to a long-lasting motor.